Comprehensive Guide to Pipeline Welding Inspection: Ensuring Honesty and Safety in Pipeline Building and Upkeep
The honesty and security of pipes are critical in today's infrastructure landscape, underscoring the critical function of welding examination in pipeline building and maintenance. Pipeline Welding Inspection. The complexities entailed in welding evaluation raise significant questions about sector standards and the evolving innovations that might redefine these methods.

Significance of Welding Assessment
Welding inspection plays a vital role in making sure the stability and safety and security of pipeline systems. It acts as an essential procedure that validates the high quality and integrity of welded joints, which are commonly one of the most susceptible points in pipe building. Through methodical analysis, assessors can recognize prospective defects such as cracks, porosity, and incomplete blend, which might endanger the architectural stability of the pipeline.
The importance of welding evaluation expands beyond plain compliance with market criteria; it also safeguards public health and wellness and the environment. Complete inspections can boost the long life of pipeline systems, reducing the demand for pricey repair work and downtime.
In enhancement to ensuring security and conformity, welding inspection promotes a society of quality control within companies. By focusing on examination throughout the welding process, companies can develop a reputation for dependability and quality, inevitably leading to boosted customer self-confidence and organization opportunities (Pipeline Welding Inspection). Therefore, the relevance of welding evaluation can not be overemphasized in the context of pipeline building and upkeep
Key Welding Procedures
Various welding procedures are employed in pipeline building and construction, each with its very own benefits and applications. Among the most extensively utilized techniques are Secured Steel Arc Welding (SMAW), Gas Tungsten Arc Welding (GTAW), and Gas Metal Arc Welding (GMAW) SMAW is preferred for its adaptability and capacity to do well in various environmental conditions, making it suitable for field applications.
GTAW, typically referred to as Tungsten Inert Gas (TIG) welding, is acknowledged for its capability to create high-grade welds with excellent control over warm input, making it optimal for thin-walled pipelines and stainless-steel products. GMAW, or Metal Inert Gas (MIG) welding, uses high deposition rates and is efficient for large-scale projects, frequently utilized in the manufacture of pipelines in controlled settings.
Furthermore, Submerged Arc Welding (SAW) is used for its deep infiltration and high performance, specifically in the building and construction of large-diameter pipelines. Each of these procedures adds to the overall integrity and safety of pipeline constructions, allowing welders to select one of the most suitable approach based upon product type, task demands, and environmental problems. Understanding these key welding procedures is crucial for efficient pipeline welding evaluation.
Typical Issues and Their Impact
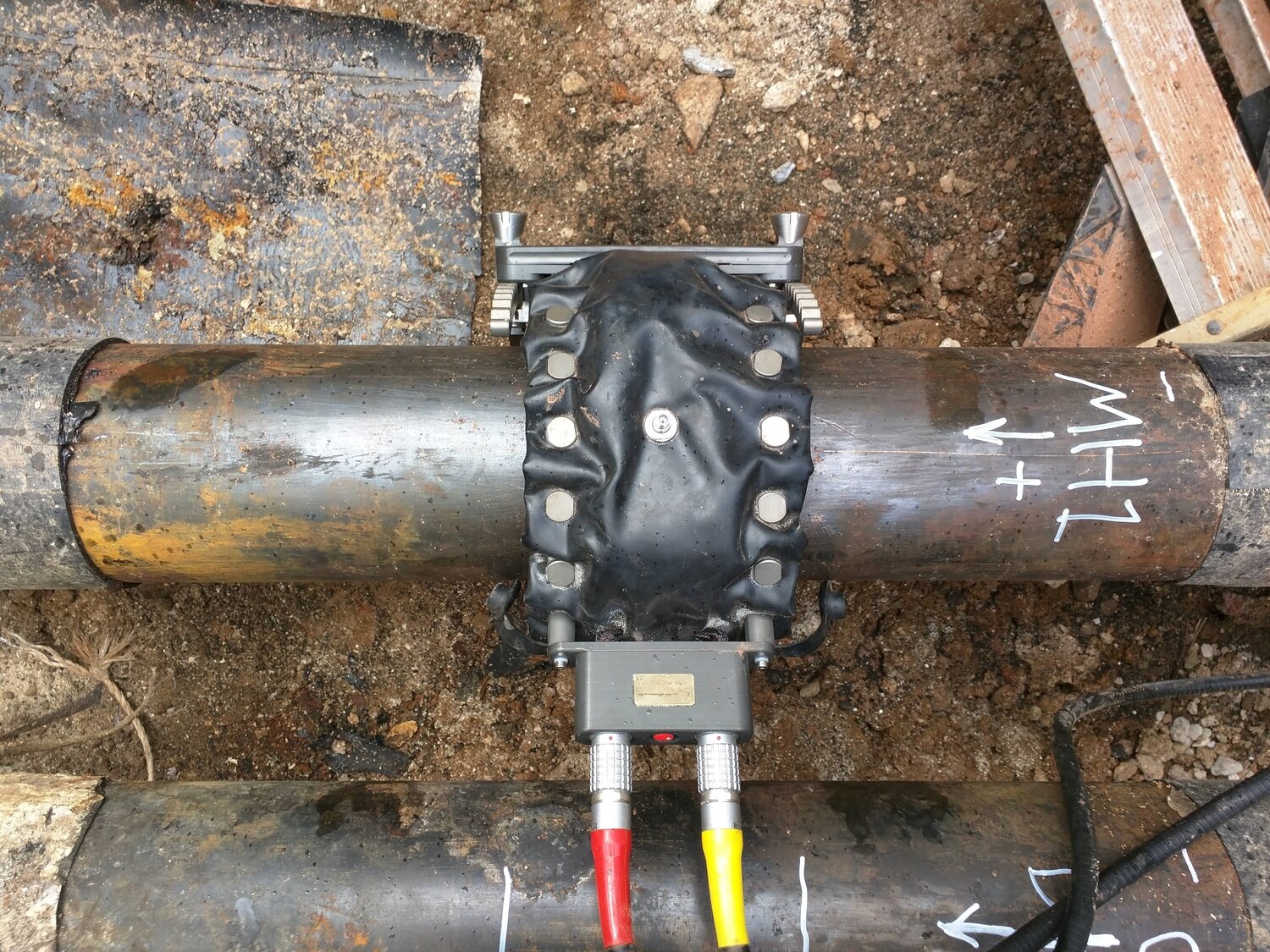
Porosity, defined by tiny gas pockets trapped within the weld, damages the material and can cause leaks. Splits, which may occur because of thermal stress and anxieties or inappropriate air conditioning, can circulate and result in structural failing under stress. Damaging, where the base steel is deteriorated along the weld grain, lowers the effective cross-section of the pipeline, boosting the threat of fracture.
Incomplete fusion happens when the weld metal does not appropriately bond with the base steel, resulting in weak locations that may fail under anxiety. Slag incorporation, the entrapment of non-metallic product within the weld, can additionally weaken the joint's integrity. Determining and dealing with these problems early click resources in the building and construction process is essential to ensuring the long-lasting reliability and safety and security of pipeline systems, therefore securing both the atmosphere and the facilities.
Evaluation Tools and methods
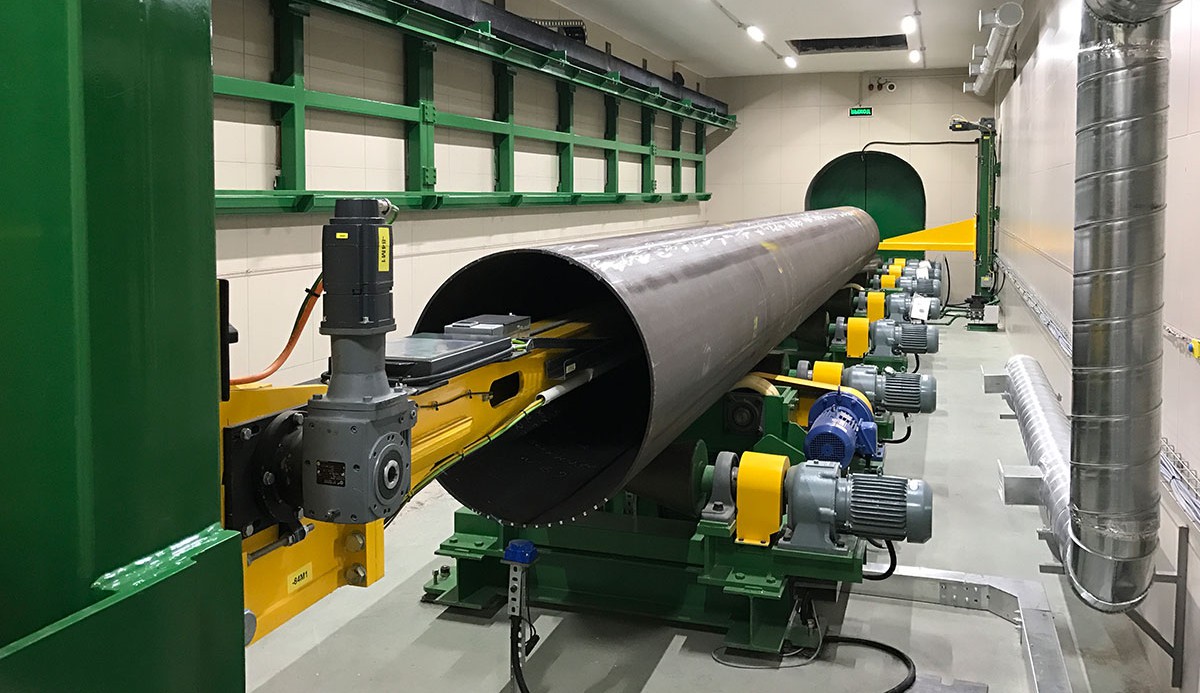
Aesthetic examination is the initial line of defense, enabling inspectors to identify surface area irregularities, misalignment, or other visible defects. Ultrasonic testing employs high-frequency acoustic waves to discover internal problems, offering exact deepness dimensions and defining issues without harming the weld. Radiographic screening uses X-rays or gamma rays to create photos of the weld, enabling the recognition of internal spaces, fractures, or incorporations.
Magnetic particle testing is specifically efficient for discovering surface area and near-surface interruptions in ferromagnetic products. This technique entails using a magnetic field and great iron bits to the weld, disclosing problems with the accumulation of bits at imperfection sites.
In enhancement to these techniques, specialized devices such as automated ultrasonic screening equipment and digital radiography systems boost inspection accuracy and performance, making sure a comprehensive analysis of pipe welds during building and upkeep.
Ideal Practices for Compliance
Abiding by ideal methods for compliance in pipe welding inspection is crucial for making certain the honesty and security of the infrastructure. Organizations should establish a thorough high quality administration system that aligns with sector criteria such as ASME, API, and AWS. This includes establishing detailed welding procedures that specify the techniques, materials, and qualifications required for welders.
Routine training and qualification of inspection workers are important to maintain high competency levels. Inspectors need to recognize with different non-destructive testing (NDT) methods, consisting of ultrasonic screening, radiographic testing, and visual examination, to properly recognize prospective problems.
Documentation plays a vital duty in conformity; preserving precise records of assessments, weld treatments, and workers certifications aids to make certain traceability and accountability. Arranged audits and testimonials of welding practices ought to click this site be carried out to determine locations for improvement and make sure adherence to established procedures.
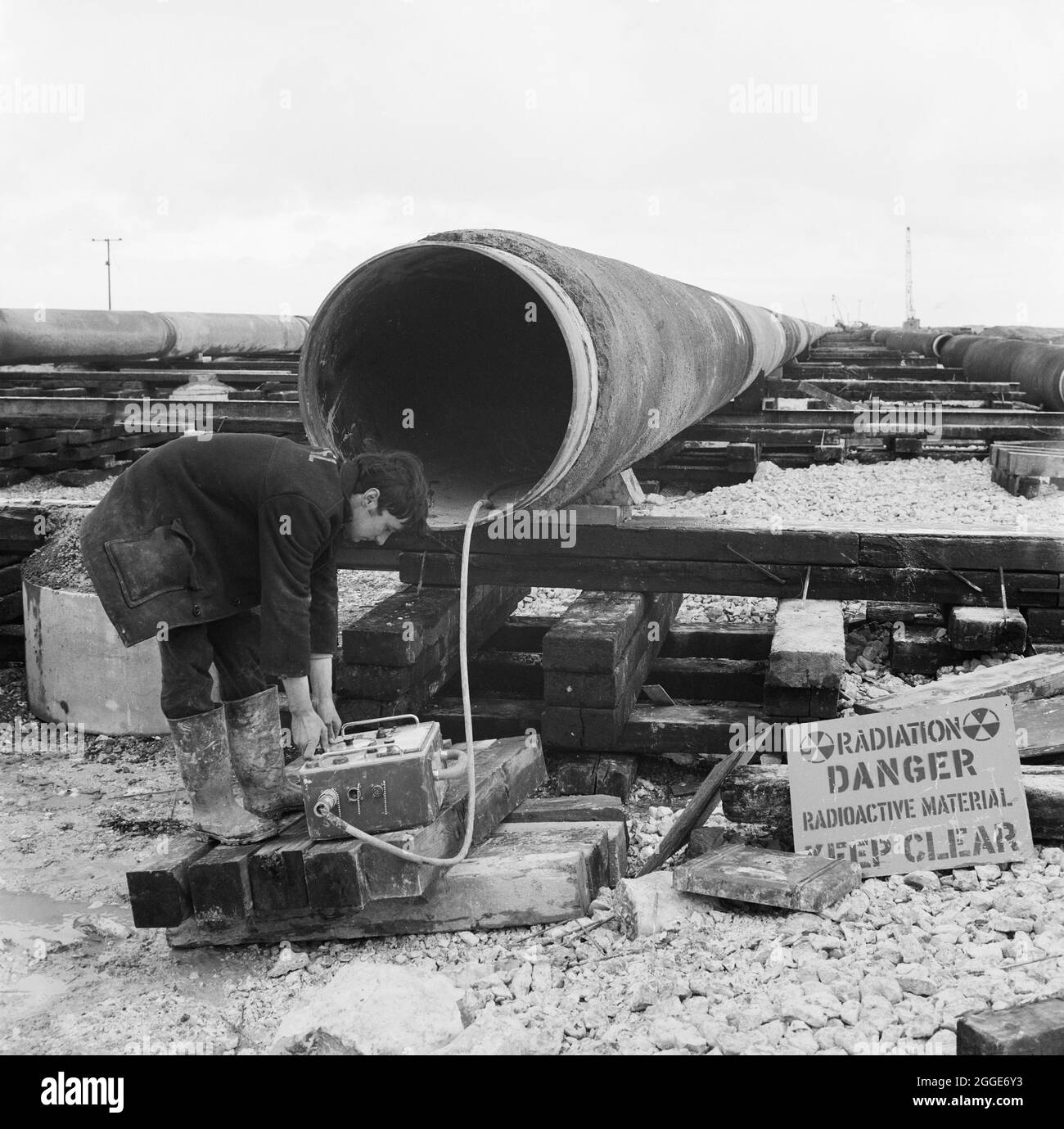
Verdict
In final thought, the application of rigorous welding assessment protocols is critical for making certain the honesty and security of pipeline construction and upkeep. Constant renovation in examination procedures will certainly add to the long life and dependability of pipe systems, highlighting the critical duty of welding assessment in the market.
The integrity and security of pipelines are extremely important in today's facilities landscape, highlighting the important duty of welding assessment in pipeline construction and upkeep. Recognizing these crucial welding processes is essential for reliable pipe welding examination.
Adhering to best practices for conformity in pipe welding evaluation is essential for ensuring the honesty and safety of the framework.In final thought, the implementation of extensive welding examination procedures is paramount for web link making certain the stability and safety and security of pipe construction and maintenance. Continuous enhancement in assessment procedures will certainly add to the durability and integrity of pipeline systems, underscoring the important duty of welding evaluation in the market.